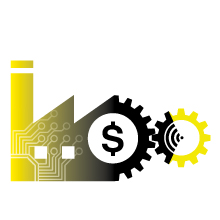
Manufacturing & Supply Chain
SYMPAN supply services on the following sectors:
Factory Supply Chain
System configuration:
- Coding of raw materials, work-in-progress and finished goods
- Master data definition
- Bill of materials
- Material movements posted in the system (goods receipt, goods return, post-production, stock in transit, stock adjustment)
- Supplier/Vendor Management Inventory (SMI/VMI)
- Supplier/Vendor Owned Inventory (SOI/VOI)
Data analysis:
- Production planning and detailed scheduling (PPDS) generating requirements in raw materials and resources
- Micro-planning optimization
- Scheduling coordination of the production departments
- Raw materials planning based on master data (minimum order qty, rounding value, lead time, safety stock)
- Capacity planning
- Production planning segmentation analysis
- Headcount planning
- Inventory monitoring, control and optimization
- Material losses monitoring and reduction
- Portfolio analysis: Pareto, Simplification, Negotiation, Cost savings
Product Costing
- Materials standard cost
- Activities definition
- Activities standard cost
- Product families
- Activities quantity per product family
Finance Planning, Monitoring, Analysis and Control
System configuration:
- Definition of cost centers and general ledger accounts
- Distinguish general ledger accounts to fixed and variable
- Invoice matching with cost centers and general ledger accounts
- Cost centers and general ledger accounts matching with product cost activities
- Cost allocation rules
Data analysis:
- Budget planning based on volume forecast
- Capacity analysis
- Budget review
- Variances analysis
- Spending control
- Utilities monitoring and control
- Cost reduction / Savings program
Shopfloor Reporting
- Overall Asset Effectiveness Model
- Planned and unplannced downtime monitoring
- Productivity per equipment / production area / work center
- Throughput per time and people resources
- Smart Factory - Online shopfloor reporting
Manufacturing Continuous Improvement - Kaizen
- Unplanned downtime root cause analysis
- Bottleneck analysis per production area / work center
- SMED analysis and changeover time reduction
- 5S and Visual factory
- Daily improvement
- Autonomous maintenance
- Material losses reduction
- Energy reduction
- Cost reduction / Savings program
- Factory Operations Support Suite - Prodaxion
- Factory Operations Support Suite - Safeworks
- Factory Operations Support Suite - incidents
Business excellence
- Business process re-engineering
- Business processs tools
- Business intelligence
- ERP functions automation
New Products Project Management
- End-to-end New Products Project Management
Factory Operations Support Suite
- Standard processes and tools that offer real added value to the production process, free up resources, reduce costs, enhance transparency throughout the production process, and facilitate internal and external auditing.